Vyaire Medical Recognizes Employee Contributions to Respiratory Therapy Devices through Total Quality Management Program
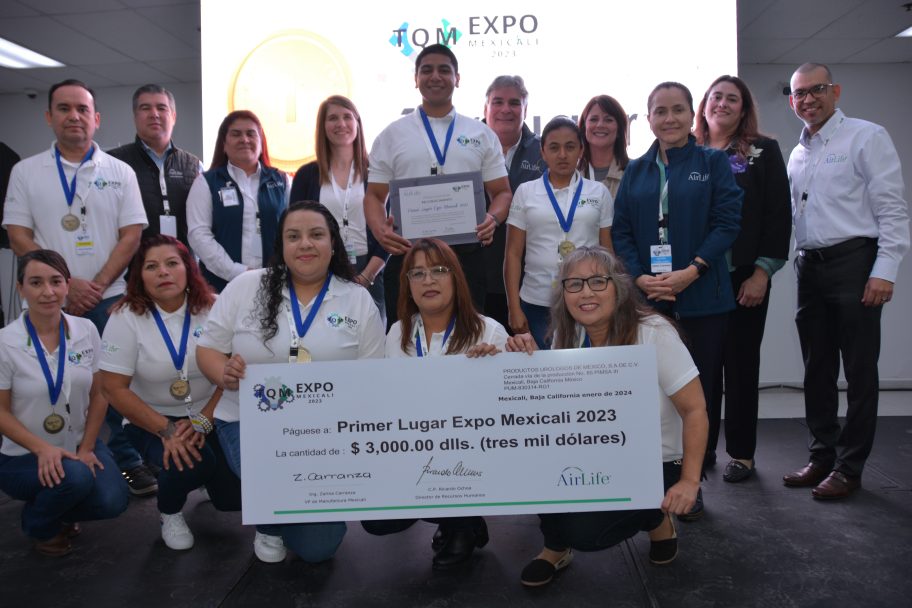
Mexicali, B.C. – Respiratory therapy is crucial for saving lives. Productos Urólogos de México has over forty years of experience manufacturing medical devices of this nature, which are vital for the survival of patients worldwide. Their products are exported to at least three continents.
For this reason, the quality of these products must be impeccable, and the management team at the Mexicali plant has developed high-performance teams that work throughout the year on various projects. These projects not only encourage continuous improvement and generate significant savings for the company but also create an awareness that their work impacts the lives of millions of people.
“I’ve always said, we are like an extension of the operating room and a hospital in general because our work affects the challenging task of saving lives. All circuits, cannulas, and other products must reach the patient with the best quality and zero defects,” stated Ricardo Ochoa, Director of Human Resources.
From this perspective, the company, now under the Airlife corporate umbrella, promotes its Total Quality Management (TQM) program both vertically and horizontally. The goal is to extend this program to plants in Nogales, Magdalena de Kino, Sonora, and Ciudad Juárez, Chihuahua.
In Mexicali, 22 teams participated in improvement projects, applying a methodology over a year in the plant that yielded significant results. Five finalist teams were selected, competing through presentations to earn financial incentives and recognition from their peers and leadership.
“Thank you to all of you who worked for a year to culminate today’s work in 2023. We are finishing the first month of 2024, and there are already teams registered on the platform. We have been implementing continuous improvement for over 15 years, developing high-performance teams, and today, more than ever, with the support of our Airlife corporate,” stated Zarina Carranza Zenteno, Vice President of Manufacturing.
Carranza Zenteno reminded attendees that this program is not only aimed at those involved in operational processes but also extends to areas such as administration and human resources.
“The mindset you have aligns perfectly with Airlife’s values, which makes me very proud to share them. I could see the passion you have for what you do and the great teamwork,” said Suzanne Kaupa, Senior Vice President of Human Resources.
FINALIST PROJECTS
-Reduce NCMRs due to dimensional problems.
-Reduce scrap N/P 57-10051 corrugated extrusion.
-Eliminate the use of N/P for leak testing.
-Reduce scrap due to contamination.
-Decrease resin scrap RPSM2Z.
This time, the savings generated by participating teams implementing their improvements over a year amounted to around $356,088. The winning teams received $3,000 for first place, $2,000 for second place, and $1,000 for third place as part of the prize pool. Luis Pons, responsible for the high-performance teams program, thanked the participation and commitment of the employees he has been working with for over a decade. They have already developed their methodology to date.